The Importance of Packaging Machine Repair for Business Continuity
The Importance of Packaging Machine Repair for Business Continuity
Blog Article
Quick and Reliable Product Packaging Maker Repair Service Provider to Minimize Downtime
In the competitive landscape of production, the effectiveness of packaging operations pivots on the reliability of machinery. Quick and trustworthy repair service solutions are vital in minimizing downtime, which can lead to significant functional obstacles and financial losses.
Importance of Timely Repair Works
Timely repairs of product packaging makers are crucial for maintaining functional performance and reducing downtime. In the fast-paced environment of manufacturing and packaging, also small malfunctions can lead to substantial hold-ups and efficiency losses. Resolving concerns immediately makes sure that machines run at their optimal capability, therefore securing the circulation of procedures.
Moreover, normal and prompt maintenance can avoid the rise of minor troubles right into major failures, which often incur greater fixing costs and longer downtimes. A positive approach to maker fixing not only preserves the stability of the tools but also enhances the total reliability of the manufacturing line.
Additionally, prompt repair work add to the longevity of packaging machinery. Machines that are serviced immediately are much less likely to suffer from extreme damage, permitting organizations to maximize their investments. This is particularly vital in markets where high-speed product packaging is crucial, as the demand for constant performance is vital.
Advantages of Reliable Provider
Trustworthy solution providers play a critical function in ensuring the smooth operation of packaging machines. Their knowledge not only enhances the effectiveness of fixings yet also adds substantially to the long life of tools.
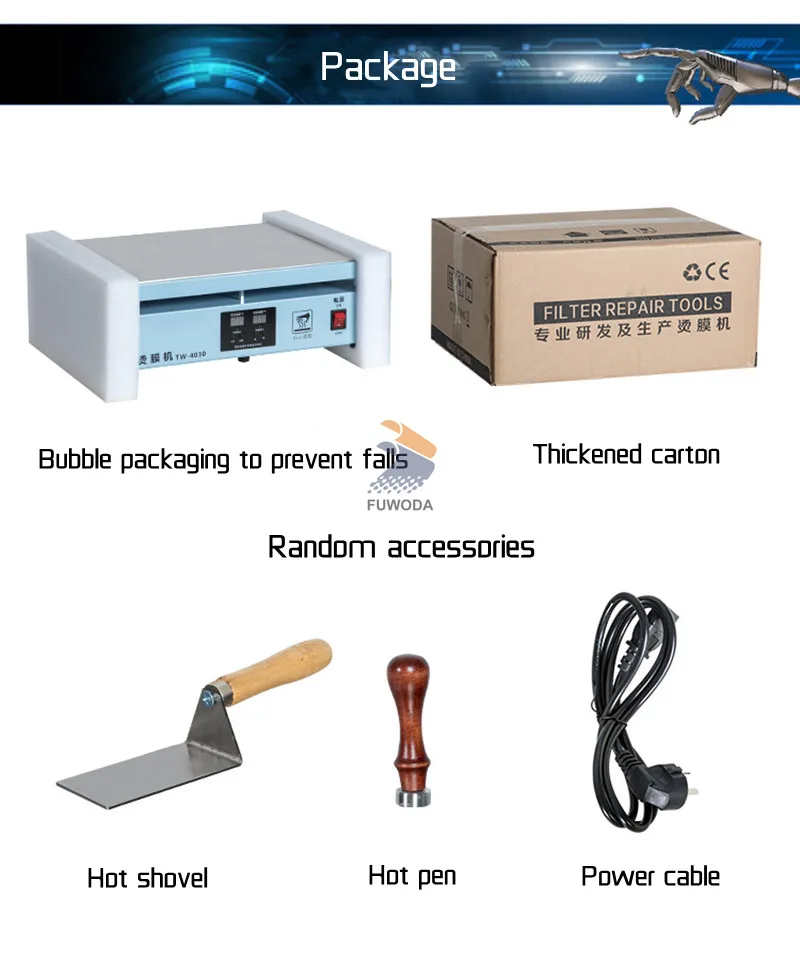
Additionally, a reliable company provides comprehensive assistance, including training and guidance for staff on maker procedure and maintenance finest practices. This not only empowers employees yet likewise cultivates a culture of safety and security and efficiency within the company. Overall, the benefits of involving reliable provider extend beyond instant repair services, favorably affecting the whole functional workflow of packaging procedures.
Common Packaging Equipment Issues
In the realm of packaging operations, numerous concerns can endanger the effectiveness and performance of makers (packaging machine repair). Another common issue is misalignment, which can trigger jams and irregular packaging, influencing item quality and throughput.
Electric problems can additionally disrupt packaging operations. Damaged circuitry or malfunctioning sensing units might cause irregular machine actions, creating delays and increased functional expenses. Furthermore, software glitches can impede the maker's shows, causing functional inefficiencies.
Inconsistent item flow is another crucial issue. This can emerge from variations in product form, size, or weight, which might influence the maker's ability to manage products properly. Insufficient training of drivers can worsen these problems, as untrained employees may not recognize early indications of breakdown or might misuse the devices.
Resolving these typical packaging equipment problems immediately is vital to keeping productivity and ensuring a smooth operation. Normal evaluations and positive maintenance can significantly mitigate these issues, fostering a reputable packaging environment.
Tips for Decreasing Downtime
To lessen downtime in packaging operations, carrying out a positive upkeep method is critical. Regularly set up maintenance checks can recognize prospective issues before they rise, guaranteeing makers run effectively. Establishing a regimen that includes lubrication, calibration, and assessment of crucial parts can significantly decrease the regularity of unforeseen break downs.
Training team to run equipment appropriately and recognize early warning signs of breakdown can additionally play a vital role. Encouraging drivers with the understanding to do basic troubleshooting can protect against small problems site from causing significant hold-ups. Maintaining a well-organized stock of essential extra components can expedite repair work, as waiting for components can lead to prolonged downtime.
In addition, documenting equipment performance and maintenance activities can aid recognize patterns and reoccurring troubles, enabling targeted treatments. Incorporating advanced surveillance technologies can give real-time information, making it possible for anticipating maintenance and lessening the danger of abrupt failings.
Lastly, fostering open interaction in between operators and maintenance teams guarantees that any type of irregularities are quickly reported and dealt with. By taking these positive steps, organizations can enhance functional performance and considerably reduce downtime in product packaging procedures.
Selecting the Right Repair Work Solution
Picking the proper fixing solution for packaging devices is a critical choice that can substantially influence operational performance. Begin by evaluating the service provider's experience with your particular kind of product packaging equipment.
Following, think about the company's track record. Seeking feedback from other organizations within your sector can offer insights into dependability and top quality. Qualifications and collaborations with identified devices manufacturers can additionally indicate a dedication to quality.
Additionally, analyze their response time and accessibility. A provider who can use timely assistance decreases downtime and keeps production flow constant. It's also vital to ask about guarantee and solution assurances, which can mirror the self-confidence the provider has in their work.

Final Thought
Finally, the value of dependable and quick product packaging machine repair services can not be overemphasized, as they play a crucial duty in minimizing downtime and ensuring operational efficiency. By focusing on timely repairs and selecting reliable provider, organizations can effectively deal with typical problems and maintain productivity. Applying positive maintenance techniques and purchasing personnel training more enhances the longevity of packaging equipment. Ultimately, a strategic method to fix services cultivates a more durable production setting.
Prompt fixings of packaging makers are essential for keeping operational performance and decreasing downtime.Additionally, prompt repair services contribute to the long life of product packaging machinery. Generally, the advantages of involving Look At This dependable service providers prolong beyond instant repair work, positively impacting the whole operational process of packaging processes.
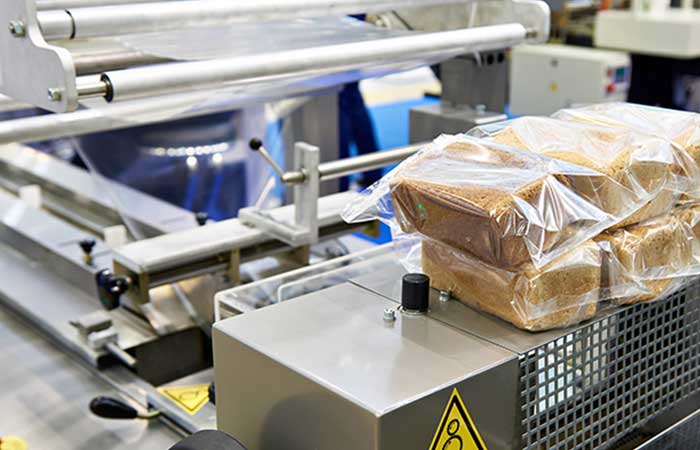
Report this page